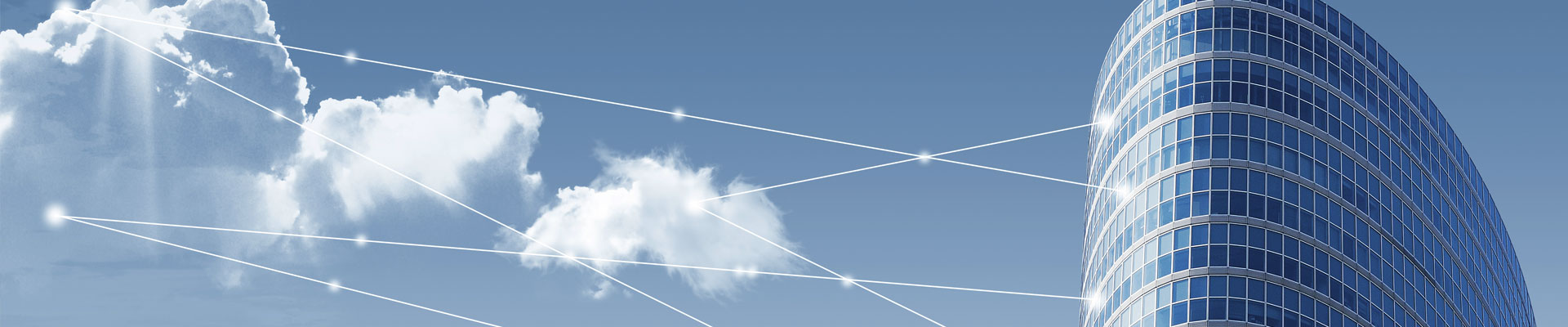
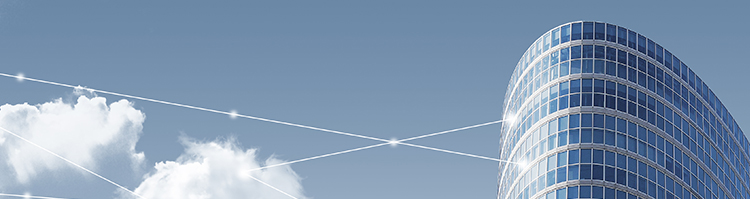
SMT貼片加工中常見的工藝缺陷
隨著越來越多的設(shè)計(jì)使用帶有表面貼裝焊盤的較小元件,由于各種設(shè)計(jì)和制造問題,表面貼裝技術(shù)(SMT)的工藝缺陷會(huì)造成安裝并影響良率。這些問題過去可能很小,對(duì)產(chǎn)量的影響可忽略不計(jì),但它們可能導(dǎo)致返工成本迅速增加,在現(xiàn)在應(yīng)該避免這些問題的出現(xiàn)。這是在設(shè)計(jì)和組裝過程中可以避免的一些基本SMT工藝缺陷。下面就跟著smt貼片加工廠家一起來看一看吧。
一、墊之間的橋接
橋接在低粘度焊料中很常見,并且會(huì)導(dǎo)致相鄰焊盤之間的短路。當(dāng)溫度超出理想的焊接范圍時(shí),也會(huì)發(fā)生這種情況,從而導(dǎo)致潤濕性差或芯吸過多。解決此問題的關(guān)鍵是在焊盤(即非焊盤定義的SMD焊盤或NSMD)周圍放置防焊墊凸版。該浮雕提供了多余的焊料可吸入的空間,有效地阻止了焊料在兩個(gè)相鄰焊盤之間流動(dòng)。這類似于球形柵陣列(或BGA)組件及其狗形扇形通孔之間的阻焊層壩。用于防止橋接的NSMD焊盤及其阻焊層凸版的側(cè)視圖。NSDM焊盤和阻焊層之間的間隙為多余的焊料提供了空間。
二、去濕
去濕是涉及選擇焊膏的問題。水溶性無鉛焊錫膏很少發(fā)生此問題,盡管在焊接到HASL涂飾劑上時(shí),鹵化物基焊膏可能會(huì)發(fā)生此問題。如果導(dǎo)體表面被嚴(yán)重氧化或焊膏已失效(即助焊劑無效),也會(huì)發(fā)生這種情況。使用高度活化的焊膏將使您的焊料在組裝過程中與焊盤形成牢固的結(jié)合。您還應(yīng)確保很大程度地清除了要連接的金屬上的所有氧化物。這將防止表面張力在固化過程中將焊料拉過焊盤并進(jìn)入球中。
有助于防止?jié)櫇竦倪^程的另一部分是在焊接過程中使氮?dú)饬鬟^回流爐。這有助于防止高溫烤箱中形成氧化物。您還應(yīng)該檢查電鍍厚度是否足夠(至少5微米)。兩種措施都有助于防止在焊接過程中氧化物的形成和擴(kuò)散到鍍層中。
三、無鉛焊料潤濕不良
無鉛錫銀銅焊料對(duì)于保持RoHS符合性很重要,但是在裸銅上焊接時(shí)潤濕性較差。這是在裸露的導(dǎo)體上使用表面處理的眾多原因之一。錫,銀和ENIG的表面光潔度可提供更好的潤濕性。
焊接過程中的峰值溫度也應(yīng)在正確的范圍內(nèi)。無鉛錫銀銅焊料的適合工作溫度約為240°C,超出此范圍的焊接會(huì)導(dǎo)致潤濕性問題。
四、組件移動(dòng)和邏輯刪除
墓碑也是與潤濕性有關(guān)的問題。在理想的焊接工藝中,熔融的焊料會(huì)同時(shí)潤濕SMT組件的所有焊盤。如果一側(cè)的焊盤先于部件的另一側(cè)的焊盤潤濕(即達(dá)到足夠高的溫度),則焊料將在凝固時(shí)拉動(dòng)部件。組件兩側(cè)的力不匹配會(huì)導(dǎo)致組件的一側(cè)從墊板上略微提起或偏離墊板上的理想位置。在某些情況下,盡管接觸電阻可能很高,而結(jié)合力很弱,但該組件仍會(huì)通過焊料保持附著在焊盤上。
在溫度不匹配的情況下,例如組件的一端根本不潤濕,這可能導(dǎo)致組件站在一端,這稱為墓碑。這是SMT電阻器和電容器中的常見問題。回流焊接過程中的墓碑現(xiàn)象對(duì)應(yīng)多種可能的原因。常見的原因是回流爐中的溫度不均勻,這可能導(dǎo)致PCB不同區(qū)域的焊料比其他區(qū)域的焊料更早潤濕。組裝過程中焊膏的不均勻涂抹還可能導(dǎo)致整個(gè)電路板的潤濕變化。
在設(shè)計(jì)方面,具有不均勻排列的焊盤的組件組在回流焊接過程中易受潤濕和墓碑影響。焊盤的大小也會(huì)影響其在回流焊接過程中的溫差;較大的焊盤需要更多的熱量才能達(dá)到定義的溫度,因此,在組件的每一側(cè)都應(yīng)使用大小相等的焊盤。定義焊盤尺寸時(shí),很容易使焊盤過大,并且多余的銅會(huì)在焊接過程中散熱。
以上就是小編給大家介紹的有關(guān)于smt貼片在焊接期間應(yīng)避免的常見工藝缺陷,希望在看完之后能夠?qū)Υ蠹矣兴鶐椭=⒉季謺r(shí),請(qǐng)務(wù)必檢查焊盤的尺寸和間隙,以確保組裝時(shí)的可焊性。眾所周知,在組件的較冷側(cè)使用散熱片有助于防止回流焊接過程中的墓碑。請(qǐng)注意,帶有散熱片的焊盤和通孔具有類似于真實(shí)電容器的復(fù)雜阻抗結(jié)構(gòu),在高速/高頻設(shè)計(jì)中會(huì)產(chǎn)生一些信號(hào)完整性問題。
一、墊之間的橋接
橋接在低粘度焊料中很常見,并且會(huì)導(dǎo)致相鄰焊盤之間的短路。當(dāng)溫度超出理想的焊接范圍時(shí),也會(huì)發(fā)生這種情況,從而導(dǎo)致潤濕性差或芯吸過多。解決此問題的關(guān)鍵是在焊盤(即非焊盤定義的SMD焊盤或NSMD)周圍放置防焊墊凸版。該浮雕提供了多余的焊料可吸入的空間,有效地阻止了焊料在兩個(gè)相鄰焊盤之間流動(dòng)。這類似于球形柵陣列(或BGA)組件及其狗形扇形通孔之間的阻焊層壩。用于防止橋接的NSMD焊盤及其阻焊層凸版的側(cè)視圖。NSDM焊盤和阻焊層之間的間隙為多余的焊料提供了空間。
二、去濕
去濕是涉及選擇焊膏的問題。水溶性無鉛焊錫膏很少發(fā)生此問題,盡管在焊接到HASL涂飾劑上時(shí),鹵化物基焊膏可能會(huì)發(fā)生此問題。如果導(dǎo)體表面被嚴(yán)重氧化或焊膏已失效(即助焊劑無效),也會(huì)發(fā)生這種情況。使用高度活化的焊膏將使您的焊料在組裝過程中與焊盤形成牢固的結(jié)合。您還應(yīng)確保很大程度地清除了要連接的金屬上的所有氧化物。這將防止表面張力在固化過程中將焊料拉過焊盤并進(jìn)入球中。
有助于防止?jié)櫇竦倪^程的另一部分是在焊接過程中使氮?dú)饬鬟^回流爐。這有助于防止高溫烤箱中形成氧化物。您還應(yīng)該檢查電鍍厚度是否足夠(至少5微米)。兩種措施都有助于防止在焊接過程中氧化物的形成和擴(kuò)散到鍍層中。
三、無鉛焊料潤濕不良
無鉛錫銀銅焊料對(duì)于保持RoHS符合性很重要,但是在裸銅上焊接時(shí)潤濕性較差。這是在裸露的導(dǎo)體上使用表面處理的眾多原因之一。錫,銀和ENIG的表面光潔度可提供更好的潤濕性。
焊接過程中的峰值溫度也應(yīng)在正確的范圍內(nèi)。無鉛錫銀銅焊料的適合工作溫度約為240°C,超出此范圍的焊接會(huì)導(dǎo)致潤濕性問題。
四、組件移動(dòng)和邏輯刪除
墓碑也是與潤濕性有關(guān)的問題。在理想的焊接工藝中,熔融的焊料會(huì)同時(shí)潤濕SMT組件的所有焊盤。如果一側(cè)的焊盤先于部件的另一側(cè)的焊盤潤濕(即達(dá)到足夠高的溫度),則焊料將在凝固時(shí)拉動(dòng)部件。組件兩側(cè)的力不匹配會(huì)導(dǎo)致組件的一側(cè)從墊板上略微提起或偏離墊板上的理想位置。在某些情況下,盡管接觸電阻可能很高,而結(jié)合力很弱,但該組件仍會(huì)通過焊料保持附著在焊盤上。
在溫度不匹配的情況下,例如組件的一端根本不潤濕,這可能導(dǎo)致組件站在一端,這稱為墓碑。這是SMT電阻器和電容器中的常見問題。回流焊接過程中的墓碑現(xiàn)象對(duì)應(yīng)多種可能的原因。常見的原因是回流爐中的溫度不均勻,這可能導(dǎo)致PCB不同區(qū)域的焊料比其他區(qū)域的焊料更早潤濕。組裝過程中焊膏的不均勻涂抹還可能導(dǎo)致整個(gè)電路板的潤濕變化。
在設(shè)計(jì)方面,具有不均勻排列的焊盤的組件組在回流焊接過程中易受潤濕和墓碑影響。焊盤的大小也會(huì)影響其在回流焊接過程中的溫差;較大的焊盤需要更多的熱量才能達(dá)到定義的溫度,因此,在組件的每一側(cè)都應(yīng)使用大小相等的焊盤。定義焊盤尺寸時(shí),很容易使焊盤過大,并且多余的銅會(huì)在焊接過程中散熱。
以上就是小編給大家介紹的有關(guān)于smt貼片在焊接期間應(yīng)避免的常見工藝缺陷,希望在看完之后能夠?qū)Υ蠹矣兴鶐椭=⒉季謺r(shí),請(qǐng)務(wù)必檢查焊盤的尺寸和間隙,以確保組裝時(shí)的可焊性。眾所周知,在組件的較冷側(cè)使用散熱片有助于防止回流焊接過程中的墓碑。請(qǐng)注意,帶有散熱片的焊盤和通孔具有類似于真實(shí)電容器的復(fù)雜阻抗結(jié)構(gòu),在高速/高頻設(shè)計(jì)中會(huì)產(chǎn)生一些信號(hào)完整性問題。
江西英特麗電子科技有限公司成立于2016年5月,坐落于人杰地靈的才子之鄉(xiāng)-江西省撫州市臨川區(qū),江西英特麗電子科技有限公司現(xiàn)有30,000平方米的廠房面積,24條SMT產(chǎn)線,8條插件線,4條波峰焊線,8條組裝線,4條包裝線,總投資10個(gè)億,配備先進(jìn)完善的數(shù)字化管理體系,致力于打造工業(yè)4.0智慧工廠。擁有完善工業(yè)4.0解決方案,PCBA加工服務(wù),SMT貼片加工服務(wù),OEM電子加工服務(wù),ODM代工代料服務(wù)。
上一篇: smt貼片加工廠的加工品質(zhì)與服務(wù)態(tài)度是生存關(guān)鍵 下一篇: pcba加工過程中的焊接要求
Copyright © 2020-2022 贛ICP備19014000號(hào)-1
贛公網(wǎng)安備36100002000168號(hào) 江西英特麗電子科技股份有限公司深圳分公司
